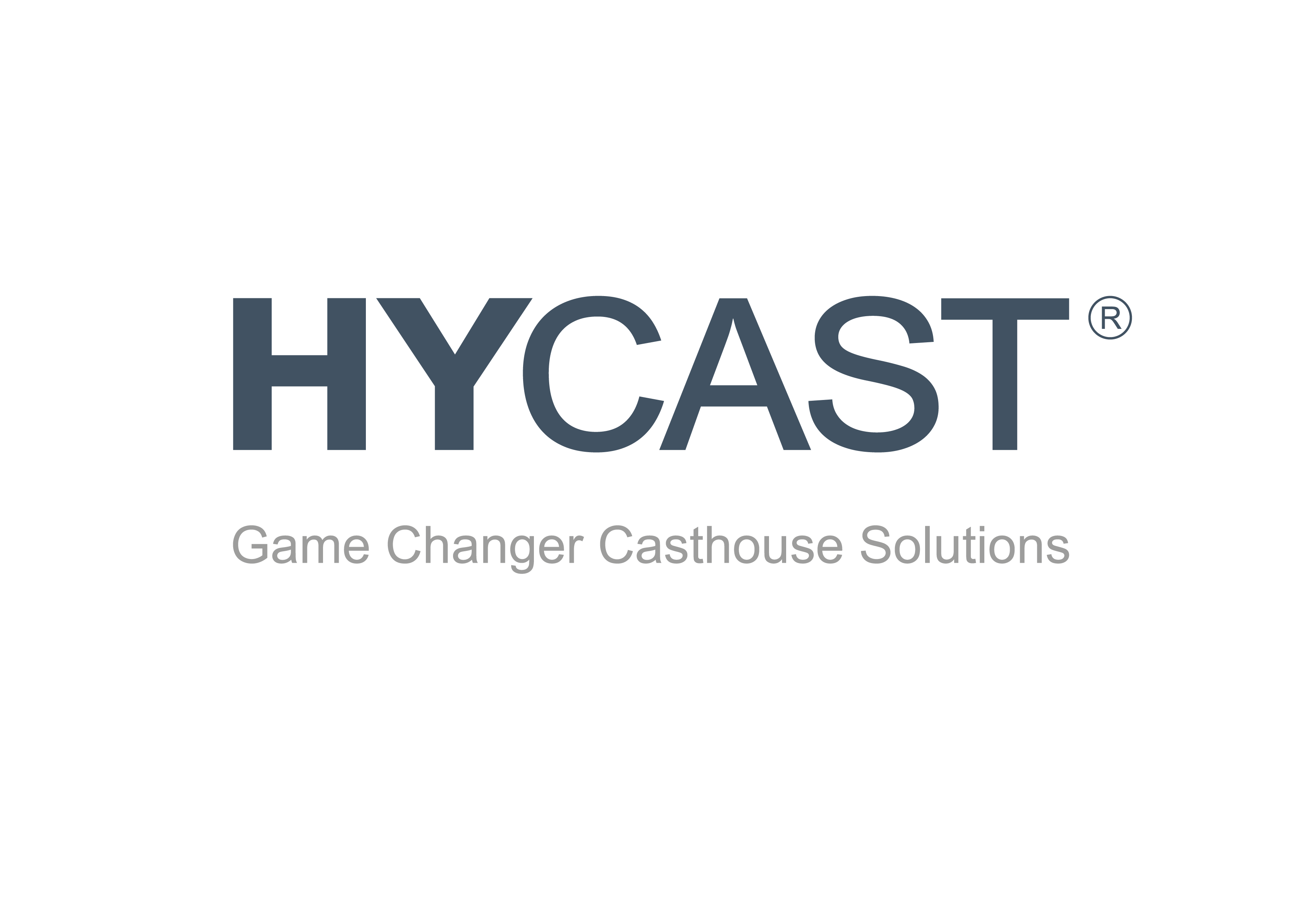
Europress manufactures modern waste compactors and balers using the Sovelia Core PLM system and Sovelia Configurator
Challenges
- Many customers needed a customised solution regarding the size, capacity, and functionality of the waste compactor.
- Designing and manufacturing customised products often took a lot of time, which extended delivery times.
- Complex and manual customisation processes increased the risk of design errors.
- Items and structures were manually created in the ERP system.
- Time-consuming processes due to many manual steps.
- Slow information flow between designers and production.
- Need for efficient product lifecycle management.
Solutions
- Sovelia Core data management system was optimised for Europress's operations.
- Sovelia Configurator is used to manage customer-specific product variants and automate design.
Benefits
- Time and effort are saved as all product data is visible in one system.
- Maintenance teams in different countries can view images, structures, and spare part needs.
- Time and effort required for creating and maintaining product units are saved.
- Design practices and quality are improved and standardized.
- The risk of human errors is reduced.
- Faster delivery times.
- Customized product design is significantly faster with Sovelia Configurator.
- Designers' work time is freed up for actual design work.
- Reviewing and approving designs has become easier.
- Information is accessible via a web interface on mobile devices.
- Designs can be automatically viewed as 3D models.
- Product documents are smoothly accessible when all product data is stored in one place.
- Order history data is accurately stored in one place and is easily accessible.